Type II anodizing of titanium by means of dark anodizing – TioDark™
If hard, scratch-resistant surfaces are required for implants and instruments made from titanium and titanium alloys, we recommend that our customers opt for the TioDark™ type II anodizing process offered by our Medical Surface Center. This process increases fatigue strength, reduces abrasive wear of the parts and creates a layer that boasts excellent biocompatibility. Dark anodizing – TioDark™ – meets the criteria for cytotoxicity (ISO 10933-3/5), hemocompatibility testing (ISO-10993-4), and HET-CAM testing (ISO 10993-4/10). The process also prevents critical alloy elements from being released. TioDark™ surfaces are ideal for laser marking. Thanks to their dark gray color and pleasant haptic properties, they also provide an interesting contrast to TioCol™ surfaces.
Dark anodizing TioDark™ – areas of application
Do you require dark anodizing TioDark™ services for your company?
Our service for dark anodizing TioDark™ of your medical products is designed for the highest requirements in medical technology sector.
Do you require dark anodizing TioDark™ services for your company?
Our service for dark anodizing TioDark™ of your medical products is designed for the highest requirements in medical technology sector.
Anodizing typ II of titanium – How it works:
With the TioDark™ process, the dark gray color is the result of a combination of the optical interference and absorption effect when light penetrates the oxide layers. Under normal ambient conditions, titanium spontaneously forms a 5 nanometer thick titanium dioxide layer. With TioDark™, the oxide layer is significantly thicker and also exceeds the layer thicknesses of TioCol™.
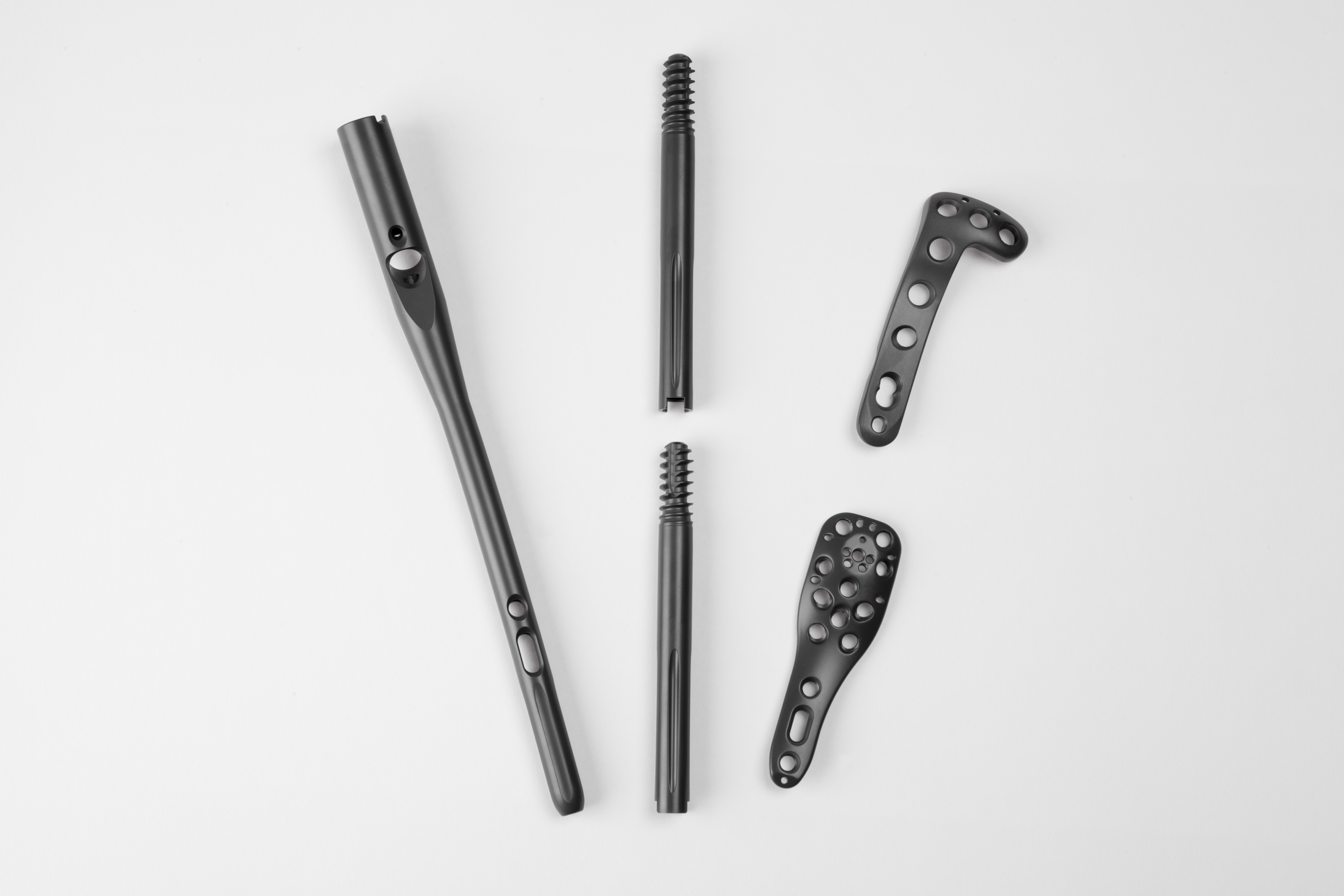
The scratch test for dark anodized titanium (Ti6AI4V)
The surface hardness, scratch resistance and fatigue strength (4-point bending test) of the processed parts are significantly improved compared to untreated parts. In addition, friction is also significantly reduced compared to other hard surfaces.
Dark anodizing using the TioDark™ process in a KKS dark anodizing unit
Dark anodizing technology
With TioDark™, the passivated oxide layer is modified by an electrochemical process (“Anodizing type II” – AMS 2488). Depending on the requirements, the implants are first pre-treated (e.g. mechanical pre-treatment and cleaning).
During the subsequent anodizing process, the thickness of the oxide layer is significantly increased electrochemically by applying an electric voltage. For this, the dental implants are electrically connected across a rack and switched as an anode in an aqueous electrolyte. Due to the particular nature of the electrolyte and process control, dielectric flashovers (sparks) are created during the process, thereby remelting the oxide layer.
Two layers form, namely a conversion oxide layer as well as a porous outer oxide layer which is removed by dry blasting after dark anodizing. The conversion layer has an average thickness of 1.0 to 1.5 µm; this is for the layer depth where the oxygen content in the oxygen gradient is 50%.