Intuitive system control for process systems
All systems and installations are designed and programmed by KKS control and software experts. Most manual and automatic process systems are equipped with IPC controllers from Siemens. KKS solutions offer the complete and manipulation-proof logging of all recipe parameters and order data. KKS systems controls are characterized by:
- Self-explanatory user interface
- Intuitive operation and multi-language capability
- Stability and reliability
- Flexible integration into existing system landscapes (production networks, ERP systems, etc.)
- Process reliability and integrated parameter monitoring
- Traceability thanks to logging
User management tailored to customer requirements with authorization levels and a connection to an existing manufacturing execution system (MES) can be implemented at any time. The integration of RFID or bar code scanners for order entry and workpiece holder detection is often an integral component of such a system. A secure remote maintenance connection is also integrated as standard, which enables KKS service technicians to support customers throughout the world.
Intuitive operation of KKS system controls
All parameters, processes and functions are controlled and monitored by the intuitive system control. The compact embedded system offers maximum reliability and can be integrated into existing networks via a wide range of standard interfaces. The start screen provides system operators with an instant overview of the current system status. All process tanks can also be opened in a detailed screen and the respective actuators (valves, drives) can be operated in manual mode.
System control performs the following functions:
- Creating or reading in recipes via a database
- User management
- Controlling and monitoring processes and parameters
- Creating a log of target and actual values with good/bad evaluation
- Records alarm messages
- Extensive visualization of treatment processes and system status
- System control operation via touchscreen
Intuitive and user-friendly menu guidance ensures easy system operation. Relevant order data can be read in quickly and without errors using a bar code or RFID scanner.
Integrated process logging:
The automatic logging of process-relevant parameters can be transferred to another system as a PDF or printed out directly from the system. These logs, which can be defined on a customer-specific basis, usually contain the following information/parameters:
- Software and version number
- Operator ID (operator level, personnel number)
- Order ID including article number, batch number, quantity
- Date and start time of the process or process step
- TARGET/ACTUAL value comparison of all process parameters
- Alarms and error messages during the process
- Operator signature field
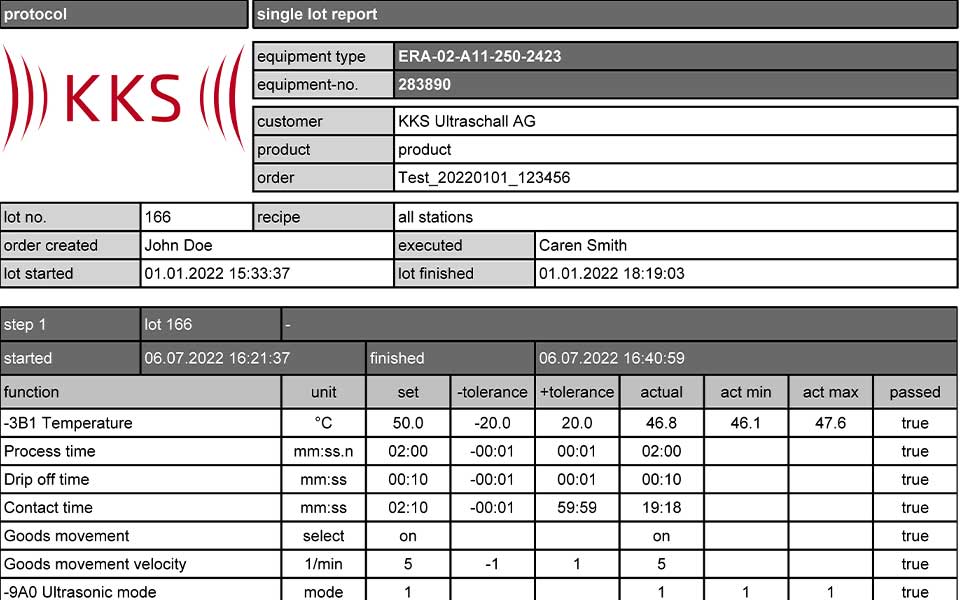
Example of a superordinate control system
KKS developed a superordinate system control for the integration of multiple production systems of a medical product manufacturer. This in turn is networking with the existing manufacturing execution system (MES).
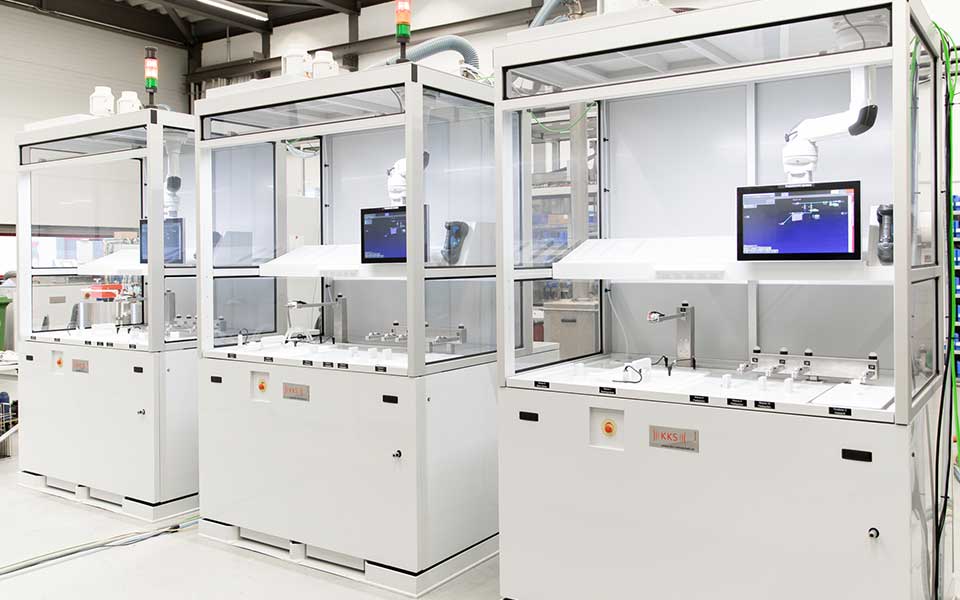
Semi-automated process modules
Production systems for pickling and electropolishing products with a superordinate control system. The precise process parameters for the treatment processes are determined automatically by an integrated weighing cell.

Fully automatic passivation system
Automatic passivation and final cleaning system with an integrated DI water circuit.
Realization of a supordinate production control system according to customer specifications
At the goods-in station, the order data is recorded in a superordinate production control system. The process data, together with all process parameters and their correct sequence, is transferred directly to all of the necessary production systems. The individual production moduls are linked by a superordinate control system and the data is exchanged between the various modules. An integrated weighing cell is the key element in this system network. The logic integrated in the control system uses the weight of the products to determine the process parameters for pickling and electropolishing and automatically forwards these to the corresponding production module. This weight-controlled sequence ensures the extremely reliable electrochemical surface treatment of the products.